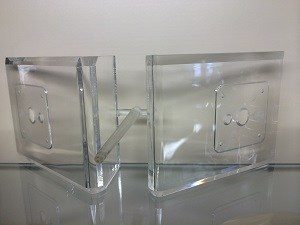
When injection molding problems appear during a production run it is usually due to a malfunction of the injection molding machine. If parts are running fine for most of the day and then things start changing, there are a few things I look at right off the bat. If the parts start coming out short, the heater bands should be checked even if the machine controller confirms all the zones are up to heat and working properly. There could be a heater band out causing a cold spot. A quick check is done by taking a scrap sprue from a PP part or comparable material and touching each heater band and also making sure the controller is calling for each zone to be on. The sprue should melt within a few seconds. If it does not, then the heater band must be removed and checked.
Splay on a part is usually caused by wet material. Many materials are hydroscopic and require drying before processing. If the dryer being used is malfunctioning, the material will not be dry which will cause injection molding problems and also the properties of the resin being used will be reduced.
During the injection molding cycle, water, oil or cartridge heaters are used to heat the mold and also cool the mold (water). If a water line gets plugged and restricts the flow, it can cause serious injection molding defects. With the mold remaining in the machine, air can be blown through the water line and most of the time will unplug it. Heating the mold is required for some resins. Some injection molds require a temperature of over 300°F so the flow of the plastic does not freeze off which will also cause short shots.
Inconsistent parts from shot to shot usually are caused by the machine. During the injection molding cycle, once the mold is closed, the initial injection phase is to fill the part and then switch in to the pack or hold stage. During this stage, the part is held under pressure by the screw. This pressure and speed are reduced. At this point, no more plastic enters the mold. This stage is the one that eliminates parts with sink and size inconsistencies.
A quick check by eye is to watch the screw come forward and stop at the pack or hold position. It should be the same every shot. If it is not, then that means you have a worn non-return valve and it must be replaced.