DESIGNING
Toth Mold/Die Inc. Since 19821. Product Development/SLA
People come up with ideas all the time either with a new invention or an improvement on an existing product. After the idea is thought of, producing it is a hard task. The average person does not know the next step to take. Toth Mold/Die Inc. can take the part concept from just an idea to a reality. Toth Mold/Die Inc. can do any part design that needs to be changed to make it an injection moldable part and also design the product to make it functional. After the design is finished, a part can be supplied in the form of a SLA at a minimal cost to test the part function and part cosmetics. Part features such as threads, snaps and types of undercuts can be replaced or improved to make producing the mold at a bare minimum cost. One of the main issues of designing a part by someone who does not have the experience in injection molding is the wall thickness which would not be suitable for injection molding. Toth Mold/Die Inc. has the experience in designing parts utilizing ribbing to allow for a moldable wall thickness.
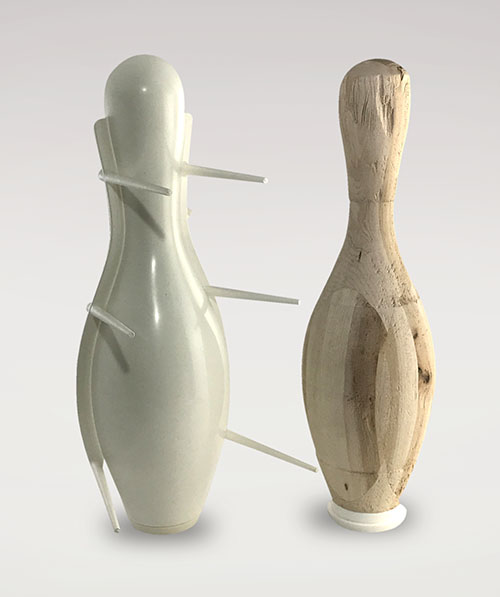
2. Mold Design
Toth Mold/Die Inc. has been designing molds for 40 years. After optimizing the part design, the next step is to have a mold built so the part can be injection molded. Some molds can be very complex due to the parting line, holes, threads and undercuts. With today’s design software, the geometry of a part can be produced without any limits. The parting line of a mold could be very complex to produce. Toth Mold/Die Inc. has the ability to design any style of parting line that is needed. Casting internal threads and any style undercut also adds to the complexity of the mold. The mold will usually require unscrewing the threads, cam action movement for slides, and gating of the part is a step that needs to be done by an experienced mold designer. Toth Mold Die Inc. has built and also runs hundreds of molds. With our experience in both injection mold building and injection molding, we can simplify your part in the design stage to make it affordable to produce.
3. Material Selection for Part Application
Material selection is one of the most complicated aspects of the final part design. The customer/inventor usually does not have enough knowledge of what type of thermoplastic material to use for their product. There are over 69,000 types and grades of thermoplastic resin. Choosing a material can be very time consuming. Toth Mold/Die Inc. has run and sampled all types and grades of thermoplastic resin from standard PP, HDPE and Nylon to very high engineered materials. Toth Mold/Die Inc. can choose a suitable resin to meet the required properties for the product. There are materials that are metal replacement and also various types of elastomers that replace rubber. There are also a large choice of fillers such as glass fiber, mineral, stainless steel and carbon fiber to mention a few. Other highly used material includes flame retardant, lubricated, conductive and optical. Another issue for a product is color. Toth Mold/Die Inc. can match any color that the customer requires and also many types of surface finishes.
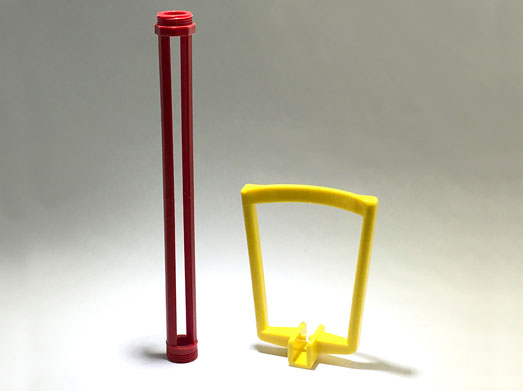
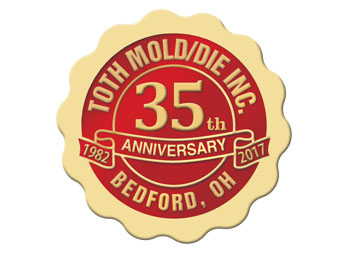